A few kilometres outside of Oslo, in a sleek business park on the banks of Oslo Fjord, is the headquarters of a company that claims to have found a new cleantech solution that will revolutionise the energy transition.
“What we have is a new patented concept which allows us to produce green hydrogen using PEM electrolysis but in a process that is much less energy-intensive, much less expensive and much safer than the current standard,” says Fredrik Mowill, founder and CEO of Hystar, the renewable hydrogen start-up in question.
The company has designed a new kind of electrolyser, which uses membrane that is one-tenth the thickness of a standard electrolyser membrane. It also ventilates the electrolysis chamber to reduce the danger of hydrogen and oxygen ever mixing, which can cause an explosion.

Hystar has received major investment from Japanese industrial giants Mitsubishi and Nippon Steel, and is already collaborating with oil giant Equinor and fertiliser manufacturer Yara on a pilot project. “Our strength is that we have a simple concept that does not involve exotic new materials or manufacturing processes,” says Mowill.
Another key technological strength of Hystar is its circular material management, which has been prioritised from the outset to help manage the ever-thorny issue of critical mineral supplies – and in particular the metal iridium, which is used to make the anode in PEM electrolysers but is only mined at a volume of around eight tonnes per year.
“Something we are doing from the onset is recycling platinum and iridium which has not been a major focus in our industry until now,” says Mowill. “We are recycling a very high percentage of platinum and iridium and can recover more than 90%.” The firm has been doing this in collaboration with its investor Mitsubishi Corporation, which is one of the largest platinum group metals (PGM) traders in the world, and also make use of PGM recycling in their work with companies in the automative industry, with catalytic converters.
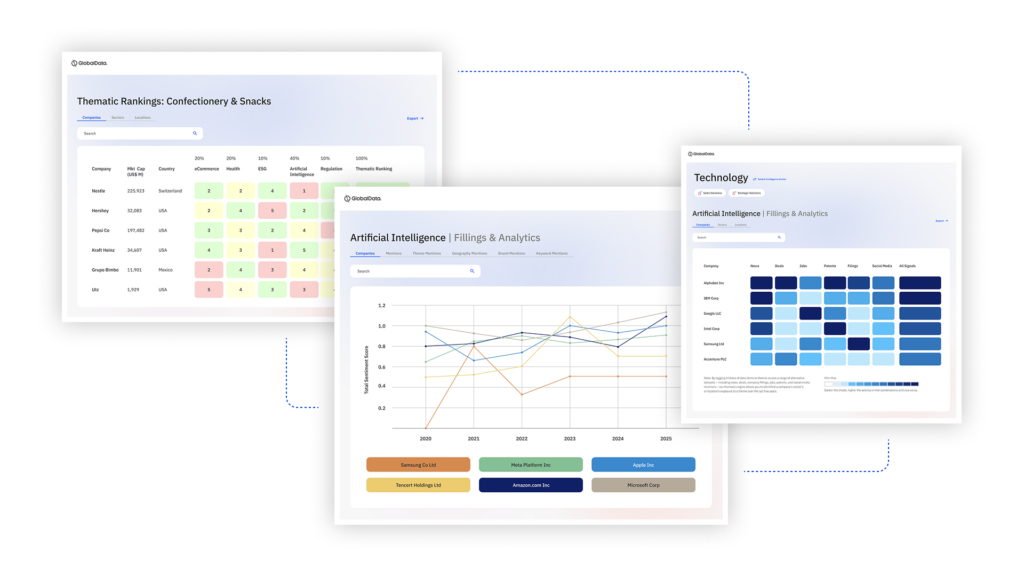
US Tariffs are shifting - will you react or anticipate?
Don’t let policy changes catch you off guard. Stay proactive with real-time data and expert analysis.
By GlobalDataThe rarity and high value of PGM in electrical components and catalytic converters means that PGM recycling is already routine, with around a 60% recycling rate, according to the International Energy Agency (IEA). As demand increases during the energy transition, there are other sources of secondary PGM – for example, premium spark plugs – which are not yet currently mined for their metals due to the low concentration of PGM.
Innovating to meet critical minerals concerns
Policymakers are rightly concerned about critical mineral supplies during the energy transition. IEA data modelling shows that lithium demand in clean energy technologies will increase more than 40-fold between 2020 and 2040 in a scenario where the world meets its climate goals under the Paris Agreement. Cobalt, graphite and nickel demand will increase around 20-fold, while manganese and rare earths demand will increase nearly ten-fold.
Rising geopolitical tensions are exacerbating security of supply concerns in the West, given that recent decades have seen China grow to dominate both supplies and processing of critical minerals. Both the EU and the US now have extensive policy frameworks in place to re-domicile mineral supplies, “but they have been slow to wake up”, says David Livingstone, a fellow in the International Security Programme at think tank Chatham House.
There is a precedent to China using its domination of critical minerals supplies for geopolitical leverage: In 2011, it forced Japan to back down in a South China Sea dispute after suddenly cutting off rare earth metal exports to the country, a mineral group of which China currently controls 90% of the world’s production.
“The need for critical minerals will be immense, and outside of China the rest of the world will struggle to fill this void,” says Corby Anderson from the Colorado School of Mines, a public research university. “Recycling will be important but the gap cannot be anywhere filled by secondary sources.”
There are reasons to be hopeful that recycling can bolster critical mineral supplies. Most metals have the potential to be recycled “without the quality being affected”, says Christina Meskers from the research company SINTEF. This means that once there is a high volume of material in the system, and recycling technologies and facilities are sufficiently developed, the world should be getting supplies also from recycling.
It is also not just PGM that currently have a substantial recycling rate: gold, nickel, silver, copper and aluminium are among metals that currently have a global recycling rate of more than 40%, according to the IEA.
Some countries, according to the World Bank, already have an aluminium recycling rate of more than 90%, showing that with enhanced policy, the situation can be dramatically improved. Not only is aluminium a key component in technologies like solar PV, but avoiding aluminium smelting via recycling is also hugely beneficial to the environment as smelting alone is responsible for around 3% of global emissions.
According to insiders, innovation in critical minerals recycling is thriving with sensor-based waste sorting technologies being developed by companies like STEINERT, and companies such as Redwood Materials and Li-Cycle receiving billions in public funding in the US to innovate in the batteries recycling space.
“When I started in this field seven years ago, recycling batteries was a pretty small business,” says Jeffrey S Spangenberger, group leader of metals recycling at the Argonne National Laboratory in the US. “Now though there are battery recycling conferences packed with people, and the US government is on the case, as the fact is that we don’t have enough materials to mine domestically to meet the needs of the energy transition.”
Technical hurdles to critical mineral recycling
However, recycling will be no panacea to critical minerals concerns. The main reason for this is that there will not be enough secondary feedstock to meet a significant share of material demand.
“Right now, only a handful of electric vehicles [EVs] and batteries have reached end-of-life," says Spangenberger. "It is going to take several decades until we reach a point where there is actually significant secondary feedstock."
World Bank analysts have modelled the share of metals that can come from recycled sources by 2050 if there was to be 100% end-of-life recycling. Aluminium, copper and nickel would see secondary supplies meet around 60% of demand.
Significant supply would still have to come from primary resources in the meantime (till recycling can contribute) – and in any case, while it is theoretically interesting, 100% recycling is a situation that Meskers maintains would be “impossible from a technical and chemical point of view”.
There are also some serious technological hurdles to boosting the recycling rates of certain metals. The 15 elements that make up the rare earth metals group, for example, collectively have only around a 1% global recycling rate. These metals are often blended together with other minerals to make things like magnets and touchscreens, and separating them has traditionally involved hazardous chemicals such as hydrochloric acid and a lot of heat.
Extracting and repurposing lithium from batteries is also extremely labour-intensive and expensive, as there are a huge range of battery formats that typically need to be manually broken down. “The expense of this process means that it will typically happen in places where human capital is cheap, which raises other concerns around ESG [environmental, social and governance],” says Chatham House’s Livingstone.
Research company Wood Mackenzie recently described battery metal recycling as a seemingly “insurmountable” challenge, involving a “tedious recycling process with little value”. Spangenberger concurs that primary battery raw materials are currently “much more cost effective” than attempting to extract them from secondary material.
A useful asset, but no panacea
Recycling is not going to eliminate the need for a new primary supply of metals as demand booms during the energy transition, but if rates are improved for more easily recycled metals, and technology improves for harder-to-recycle materials, then it will prove to be a useful asset.
“Policy will incentivise technology and innovation to come up with better circular solutions that are more cost effective,” says Patrick Molloy from the think tank RMI. “We will end up seeing a greater degree of circularity by virtue of that value thread being recognised.”
[Keep up with Energy Monitor: Subscribe to our weekly newsletter]
Other circular strategies, too, can help shore up critical mineral supplies, including reducing demand for new technologies by boosting strategies like energy efficiency or public transport incentives, as well as extending the lifetime of products such as EV batteries, which still have around 80% capacity at end-of-life, and can easily be used in less energy-intensive applications.
A 2022 report from the NGO WWF modelled that enhancing material management using the aforementioned techniques – as well as recycling – could reduce overall materials demand by more than 50% between now and 2050.
Climate scientists now widely accept that you cannot hope to achieve net zero without also achieving near zero waste. “These issues are intertwined,” says Meskers. “You need energy to power the circular economy, and you need materials to enable the energy transition.” Even if recycling cannot alone solve the critical minerals issue, it will remain a fundamental area of focus, if the world is to be true to its aims of solving the climate and ecological crises.