
The Global Cement and Concrete Association (GCCA) is comprised of the world’s leading cement and concrete companies that have committed to producing net zero concrete by 2050. Over the last three decades, the industry has reduced CO2 emissions in cement production by approximately 20%, primarily through clinker substitution and the use of alternative fuels.
The GCCA has developed an industry roadmap to further reduce cement CO2 emissions by another 25% by 2030 from the 2020 levels, including continuing to increase clinker substitution and alternative fuels usage. They also aim to improve efficiency in concrete production by investing in technology and innovation.
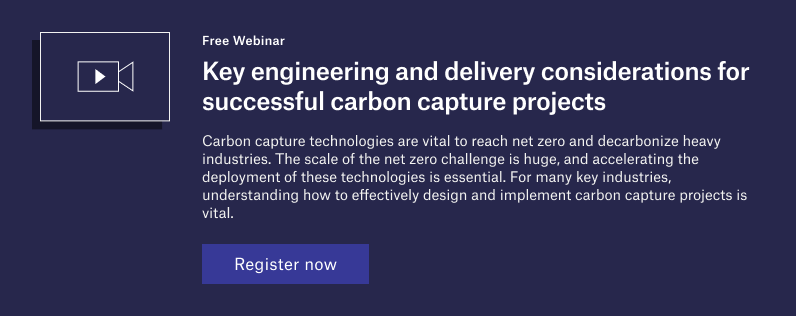
A major step in reducing CO2 will be the development and deployment of CCS technology and infrastructure. There are currently no full-scale operating CCS facilities in the cement industry, however, a Heidelberg CCS plant is in development at its cement plant in Edmonton, Canada, which is targeting startup in 2026.
Improving cement production efficiency
“Cement makes up about 12% by volume of concrete, but it contributes up to about 80% of the CO2 emissions,” explains Gary LeMaire, Senior Director of CCUS at Worley. “In Europe, the concrete mix designs are primarily driven by performance requirements, with some material ingredient specifications that allow for substitution of cement with other materials.”
“However, in the US, concrete mix designs are primarily driven by the material ingredient specifications, along with some performance measures such as compressive strength, slump and permeability.”
This means that the options for lowering the carbon intensity of concrete by substituting cement is limited. From a technical standpoint, the challenges begin with identifying and evaluating the many decarbonisation options to reduce CO2 emissions from cement production to achieve net zero.
Approximately two-thirds of CO2 emissions from cement production come from chemical process emissions, and the other third are energy related. The main driver comes from the conversion of calcium carbonate to calcium oxide, which requires a significant amount of process heat and generates CO2 as a byproduct.
According to LeMaire: “Cement producers can make incremental improvements through energy and fuel selection and energy efficiency improvements, but you can’t get to net zero without implementing carbon capture.”
“When you select which decarbonisation methods to implement, you have to consider that they are interdependent and they could potentially have effects on the cement plant’s modes of operation. When you implement carbon capture, the flue gas contaminants need to be evaluated and the pre-treatment upstream of the carbon capture unit needs to be designed properly. The provisions for utilities such as power, heat or steam, natural gas and water also need to be considered, as well as the availability of plot space.”
Commercial challenges for decarbonised concrete
“It’s unknown whether market demand for low-carbon cement will support the increased cost of production. The cost of cement production is about $30 to $80 per tonne unabated, and about $60 to $130 a tonne decarbonised, so that’s roughly double the cost,” LeMaire explains.
“With the introduction of the European Union Taxonomy, it is stated that 3/4 of cement plants in the EU are at risk of not aligning with the emissions criteria for sustainable activities risking their licenses to operate and future commercial viability.”
“Currently, the cement industry in the UK receives CO2 allowances for free, but under anticipated reform, at least half of those will need to be paid by 2030. The phase-out of the free allowances is scheduled to begin in 2026, and it’s estimated that the cumulative cost to the cement industry by 2030 could total €13 billion.”
In June 2022, the World Economic Forum published a report called Low-Carbon Concrete and Construction: A Review of Green Public Procurement Programmes, which was supported by the GCCA and includes input from public and private sectors. This report identified two important aspects of low carbon procurement, one being establishing a carbon reduction foundation and the other being procurement policies.
Decarbonisation requires collaboration
One of the recommended policies for the low carbon procurement programme is providing economic incentives. Decarbonising the cement industry requires a collaborative effort among governments, researchers, cement manufacturers, and consumers. Governments must create a conducive regulatory environment, incentivising sustainable practices while investing in research and development. Manufacturers need to prioritise innovation and implement cleaner technologies. Consumers and the construction industry can contribute by choosing environmentally friendly building materials and demanding greener options.
“The role of government certainly plays an important part,” LeMaire explains. “Then there are product technology incentives, such as the National Science Foundation and DOE grants that fund research to decarbonise cement manufacturing. In the Netherlands, SDE++ subsidises the cost of technologies that reduce emissions from heavy industry, including cement.”
Some other examples of government incentives and green public procurements include commitments made by the government to purchase a portion of the industry materials from suppliers using near-zero and zero-carbon solutions. The Clean Energy Ministerial Industrial Deep Decarbonisation Initiative (IDDI) is a global coalition working to stimulate demand for low-carbon industrial materials in heavy industries, starting with steel, cement, and concrete.
Concrete is the second-most consumed substance on earth behind water, so decarbonising the industry is crucial for the success of the energy transition. Through technological innovation and improved collaboration, reaching net zero is possible, and Worley is stepping up to lead the way to a sustainable future. Find out more in the whitepaper below.