The fundamentals of paper-making haven’t changed much in the past 2,000 years. Soak some fibre (it used to be rice, but is now mostly wood) in water, spread the slurry on a web and use a fire to dry it, while applying pressure to ensure a flat surface. What has changed, is the scale.
The paper industry, with a turnover of €90bn in the then EU28 in 2019, is Europe’s fourth-largest industrial energy user after steel, cement and chemicals. Globally, the sector accounts for 296 million tonnes of greenhouse gas emissions, making up 0.6% of the world’s total. It may not sound like a lot, but this is higher than the combined emissions of Sweden, Denmark, Finland and Norway. For this reason, it is covered by the EU Emissions Trading System, making up 4% of emissions from the sectors covered.

To make paper, you need pulp. There are two main ways to produce it, from virgin wood or from recycled material, and two main processes, chemical and mechanical. The pulp is then used to make paper, a process which uses a lot of energy.
“Making a tonne of paper uses as much energy as making a tonne of steel,” says Luisa Colasimone from the NGO Environmental Paper Network. Average energy costs are around 16% of production costs and can be as high as 30%. About 60% of the energy used by the paper industry comes from biomass and most of the rest comes from natural gas.
The good news is that the heat produced in these processes can be used to generate electricity in combined heat and power installations. In Europe, the paper industry produces about 46% of the electricity it consumes and about 18% of mills have lowered their climate impact by producing virgin pulp and paper at the same site, making production more efficient.
More savings needed
Carbon emissions in the paper industry in Europe have dropped by 29% since 2005, and there are indications of a decoupling of energy use from production, says the International Energy Agency. However, to meet the EU’s 2050 net-zero goal, the industry will have to ramp up its climate action. The Confederation of European Paper Industries (CEPI) is aiming for an 80% reduction by 2050, but even this is not enough for net zero.
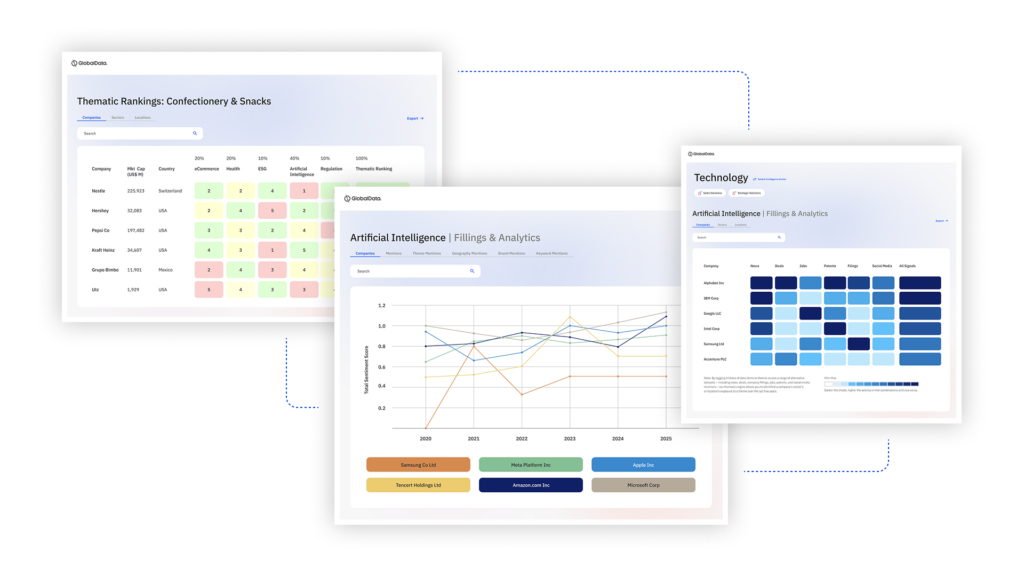
US Tariffs are shifting - will you react or anticipate?
Don’t let policy changes catch you off guard. Stay proactive with real-time data and expert analysis.
By GlobalDataElectrification appears the most promising way of creating additional emissions savings. The paper industry could be almost completely electrified with existing technologies, finds a recent paper by Silvia Maddedu at the Potsdam Institute for Climate Impact Research. “It’s not a technological issue – because the paper industry uses a lot of heat that is not particularly high temperature – it’s a cost issue,” she writes. “The technologies are there and could be implemented.”
CEPI’s director general, Jori Ringman, does not disagree but says such a switch is complicated. “Green electricity is slightly more challenging because it comes with changes in infrastructure,” he said in an interview in November. “Both for the grid, and the connection to the production side is more demanding, and so that would require more investment. But the electric boiler is comparatively inexpensive.”
Electric boilers (which are common in the Nordics) can be backups for biomass or gas generators, says Ringman. “In case of maintenance, when you take off the main boiler, you have this electric boiler as a reserve,” he explains. “Natural gas-fired plants could switch to these electric boilers. But there is the electricity price, the connection price (of a high-voltage line) and the investment needed in the connections.”
Working out just what this would mean in practice is not easy. For an industrial user in the EU, one kilowatt hour (kWh) of electricity was about four times more expensive than one kWh of gas in the first half of 2020, according to Eurostat. This suggests using electric boilers to replace heat from fossil fuels would significantly increase operating costs for the paper industry. Yet heat pump experts argue their technology can decarbonise the paper industry without breaking the bank.
Heat pump technology is already fit for use at scale in energy-intensive industries, says Alex Cohr Pachai from Johnson Controls Denmark. “The gases, compressors, valves, control valves, everything is ready,” he says. “It is just about putting it together. The temperatures [in paper-making] are higher than we normally go, but there’s no problem.”
He adds: “We install about 100 industrial heat pumps a year in Europe and if we can increase that to 1,000 or so the price will be completely different. It is a high-cost, low-volume product but, like with wind turbines, once the volume increases the price will change.”
Today, buying a heat pump is 20–30% more expensive than buying an electric boiler, estimates Cohr Pachai. But the high efficiency of a heat pump means once it is up and running its operating costs would be much lower, he argues.
Veronika Wilk, scientific project manager of the EU-funded DryFiciency project at the Center for Energy at the Austrian Institute of Technology, agrees. “Of course industry is cautious,” she adds. “So you need to do some testing and a pilot project to get things exactly right. It could take a few years before it is commercially available.”
The Austrian Institute of Technology is running three industrial trials with high-temperature heat pumps operating at 160˚C. This temperature is 20˚C lower than what is needed in the paper industry. Getting that additional 20˚C is now a major area of focus.
“Compared to conventional gas boilers, heat pumps have the potential to increase energy efficiency by up to 80%, reduce CO2 emissions by up to 75% and cut production costs by up to 20%,” says Wilk. As the carbon intensity of the grid decreases, the reduction in CO2 emissions should increase.
All-industry problem
Lowering emissions is a massive challenge for all energy-intensive industries, but while the steel and cement industries, for example, are often in the spotlight, the paper industry tends to remain under the radar. One reason for this is the argument that it, and other forest-based industries, have a broader impact on decarbonisation than just their process emissions.
The combined impact of the carbon sink of well-managed forests and the product substitution effect of using wood instead of concrete for building or paper-based textiles, means EU emissions are 20% lower thanks to forest-based industries, even after deducting process emissions, says Ringman.
The question is whether such forest management can make up for emissions from the production process. Climate campaigners do not think this argument washes.
“The paper industry is seeking to excuse itself with misleading arguments,” says Colasimone. “The impact on forests is clear-cut, often the conversion of natural forests to plantations, ending with loss of biodiversity […] and a reduction in forests’ capacity to naturally remove and store carbon safely out of the atmosphere.”
“The vast majority of paper products are short-lived,” she adds. “They are thrown away and their carbon ends up in the atmosphere within two to three years. This is the opposite of carbon storage in a mature forest or in long-lived solid wood products.”
Climate campaigners are increasingly frustrated about the lack of attention to the paper industry’s emissions, as other energy-intensive industries step up efforts to decarbonise. The paper industry is one of the few that has not committed to net-zero emissions by 2050.
At the 2021 virtual Davos Summit, 400 companies representing seven global industries – steel, cement, chemicals, aluminium, shipping, aviation and trucking – committed to work with competitors, investors, suppliers and buyers to devise “climate action agreements” by 2024 to achieve net-zero emissions by 2050. The seven industries represent about a third of the world’s global greenhouse gas emissions.
Małgosia Rybak, who leads climate change and energy issues at CEPI, insists the paper industry has made lowering emissions a core mission. “In 2019, our industry’s CEOs signed an initiative highlighting that we have a strategic interest in being at the forefront in making the decarbonisation of European society happen,” she says. “Last year, we published a 2030 manifesto, where our sector reiterates that it can contribute to reaching the 2030 goal and European carbon neutrality in 2050.”
But time is running short. Assets often have an operational life measured in decades and new fossil fuel equipment is expected to still be operational by 2050. The longer the industry waits to take action, the greater the impact of stranded assets. The good news is the industry seems increasingly aware there is significant potential for it to decarbonise by electrifying industrial processes. The hard part will be turning the necessary technology shifts from theory into reality.