Cement is the glue in the world’s most ubiquitous manmade material, concrete. Its success is due to its strength, flexibility, resilience and local availability – most cement sales are within 50–70km of production – says Jon Morrish, board member of HeidelbergCement, in conversation with Energy Monitor. Morrish is responsible for the company’s operations in western and southern Europe, and environmental, social and corporate governance (ESG).

For all its value, cement production is highly energy-intensive and in a world aiming for climate neutrality, companies like HeidelbergCement face an uphill battle to convince policymakers they can be part of a net-zero future. In September 2020, HeidelbergCement adopted a ‘beyond 2020’ strategy with sustainability as one of six core areas. Morrish says the world needs cement: “We have to decarbonise it, not demonise it.”
You have pledged to cut CO2 emissions by 30% by 2025 relative to 1990. How will this happen when two-thirds of your emissions are process-related?
We have already done a lot. We reduced our emissions by 22% from 1990 to 2019. The biggest contributor to that was a switch from burning fossil fuels to using alternative waste-derived fuels [to heat our kilns]. We also upgraded old facilities and substituted carbon-intensive raw materials for lower-carbon materials.
The next milestone is 2025, where we are targeting emissions of 525kg of CO2 a tonne (kgCO2/t) of cement produced [down from 590kgCO2/t in 2019]. That was originally our target for 2030; now we are aiming to get to less than 500kgCO2/t by 2030. This is a further reduction of 15% compared with 2019.
These are ambitious targets, but they are based on a bottom-up road map. We have built it plant by plant, country by country, across our 50 countries [of operations]. We made a detailed assessment of the challenges at each location, what we could do and how much it would cost. The whole analysis took 15 months.
Then we embedded those plans as hard targets in every manager’s bonus scheme. CO2 now represents a big part of every manager’s variable pay. And in our company, variable pay is a big piece of overall remuneration.
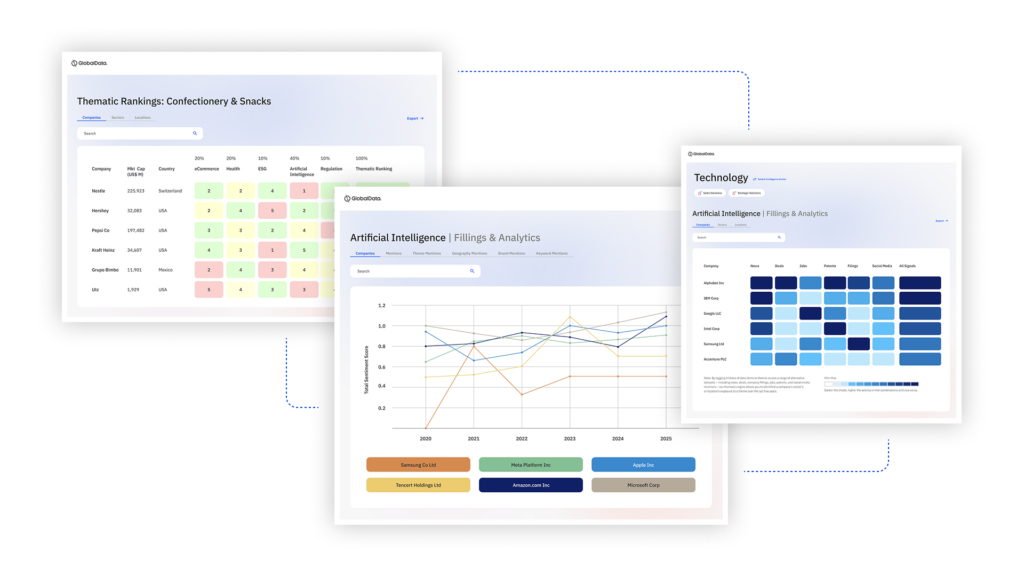
US Tariffs are shifting - will you react or anticipate?
Don’t let policy changes catch you off guard. Stay proactive with real-time data and expert analysis.
By GlobalDataThis brings real focus. “Oh, you are serious”, people suddenly think. Our view was: unless it hits our team’s wallet, we can be accused of talk not action.

How will you accelerate emission reductions out to 2030?
We will pull on the four ‘conventional’ levers that have already delivered. First, we intend to double our switch from fossil fuels to using waste-derived alternative fuels as an energy source. Globally, about 25% of our fuel is waste; we will double that by 2030. Our Lixhe plant in Belgium, near Liège, already runs on 95% waste.
The numbers are high in Europe because of a policy put in place 20 years ago: the EU waste directive. This essentially puts a high price on landfill and we have taken full advantage of that. We have worked with member states to divert municipal waste to cement kilns. A cement kiln at 1,450°C is the safest, most efficient incinerator on the planet.
Not everybody is as progressive as European policymakers. Less progressive waste policies in the US, for example, mean we only use about 10% waste-derived alternative fuels.
The second lever is upgrading old facilities. We still have a number of older technology plants we are replacing in the US, Europe and Asia. Third, we are pushing hard to convince customers in the construction sector to buy low-carbon concrete. And fourth, we make as much use as possible of low-carbon raw materials [such as slag from the steel industry] to replace carbon-intensive clinker.
Why did you move your 2030 CO2 target forward to 2025?
We have made strong progress until now. We recognise we have a responsibility. We want to be part of the solution. The world should not want to stop using concrete. It is the core of the built environment. We need to decarbonise it.
Your Polish subsidiary and German renewables company BayWa r.e. recently signed a power purchase agreement (PPA) for electricity from the Witnica Solar Park, which will be Poland’s largest solar installation. How does this fit in?
All the levers I talked about are for scope 1 [direct] emissions, which make up the lion’s share of our emissions profile. But we also need to bring down scope 2 [indirect] emissions. The kilns burn fuel, but every other process is electric and in particular grinding the clinker into cement is very electricity-intensive. We are big power users so there is a big push to move to renewable power. We have four or five solar farms at our European plants and numerous wind farms, but we are also working with PPAs.
Your ultimate goal is to make carbon-neutral concrete by 2050. How?
For this, we are focusing on a new set of levers. First, carbon capture and use, or storage (CCUS). This is a big area of focus because two-thirds of our emissions are process emissions. There is an inevitable need to capture CO2, use it if possible and store it if not.
Second, recycling construction material. Far too much demolition waste still goes to landfill, unlike municipal waste. We want to put that material back into production as a substitute for virgin materials.
Third, ‘recarbonising. It sounds strange but it works. When you produce concrete, it absorbs CO2. Over the lifetime of a building, recarbonation is a really important part of decarbonisation, and when you demolish a building, how you do that also has a big impact on how much CO2 it can absorb.
Fourth, electrifying kilns. We have trials going on. Instead of using fuels to generate the necessary heat of 1,450°C, we can electrify with renewables. This is another step change.
We are working on these new technologies in parallel with the day-to-day push on conventional measures. If you put it all together, we will be able to get to net-zero carbon concrete by 2050 or before.
What are your plans for CCUS?
There has been a big focus on the North Sea and a secondary focus on the Irish Sea, with the governments of Norway, the Netherlands and the UK. We have been involved for quite a few years. The CCS project at our Brevik plant in Norway is the first industrial-scale CCS project in the cement industry. ‘Industrial scale’ means it will capture 400,000 tonnes of CO2 a year.
[Keep up with Energy Monitor: Subscribe to our weekly newsletter]
Our part of the project – building and operating the carbon capture plant, liquifying the CO2 and putting it on ships – required extensive Norwegian government funding to go ahead. We got confirmation of this in December 2020. So it is all systems go. Construction has already started and will be finalised by the end of 2023. We intend to go live in 2024. We will supply the CO2 to the Northern Lights consortium that will take it into the North Sea.
Is there a business case for CCUS? In Brussels, we often hear it needs an EU carbon price of around €100 a tonne. Today it is approaching €40 a tonne.
Doing something like this at an industrial scale is the real challenge. Only then can you understand the real cost and know if there is a business case. We have lots of calculations and estimates but only by doing it will we know if it really works. The big unknown is the operating cost – this is very hard to judge until you build it.
We are, however, quite optimistic that these costs are manageable, as we are getting many positive signals from policymakers about instruments that would compensate for the higher operational cost of climate-friendly technologies.
CCUS has been focused on north-western Europe. What are your plans for eastern Europe?
We have two or three projects we want to put forward for funding from the EU Innovation Fund in 2021. We have spoken to the European Commission and they are keen to see eastern European projects.
From the Commission and member states we need support for storage. We need local politicians to say this is good, this is safe, let’s take this forward. It is easy to dump CO2 in the North Sea; it is not so easy to put it into old coal mines. However, to decarbonise energy-intensive industries, we need to get our heads around storage. Early movers have the potential to become world leaders in industrial decarbonisation.
There is an emerging debate about CCU. How much CO2 can be used versus stored?
We are pursuing several CCU projects at the moment. The options for CCU are manifold, from using it in our own industry to partnering with others. We are exploring enhanced oil recovery in Canada, the use of CO2 in food and industry, and we have a pre-industrial scale project in algae [that feed on CO2], where we produce pet food, in Morocco.
On top of that, we are investigating the use of CO2 for power-to-X (PtX) in combination with hydrogen, to create synthetic fuels. This is potentially the biggest use case. We are working on a PtX project with support from the German and Moroccan governments that would take hydrogen from renewables-powered electrolysis and combine it with CO2 to make synthetic fuels.
What is crucial for us is what gets classified as use versus storage, and how that feeds back into the EU Emission Trading System (ETS). If we use carbon to make industrial gases or synthetic fuels, this does not currently count as carbon reduction – but the question is what will drive climate-friendly behaviour? Every use of CO2 needs to be examined for its climate impact, economic case and to whom it is creditable.
What is your number one policy ask?
We need policymakers to recognise that the material we produce is essential. When she launched the EU’s green recovery plan, European Commission President Ursula von der Leyen said people should build in timber. You can’t build many railways or tunnels in timber. We want policymakers to work with us to decarbonise the material at the core of our built environment.
We have spent a lot of time, effort and money trying to find substitutes for our product. To a small extent, they are available, in niche areas. However, nothing has been found that has the same properties, is available locally in such quantities and can be produced at the same cost as concrete. We have to decarbonise it, not demonise it.
What climate and energy policies do you need to go carbon neutral by 2050?
In Europe, the key question is whether we will get a carbon border adjustment mechanism (CBAM). We support the EU ETS and a gradual removal of free allowances, but it needs to go hand in glove with a CBAM to ensure we have got a level playing field.
We have cement plants in Turkey and North Africa. Without a CBAM it would make sense to close down European production and increase production from these neighbouring countries – especially if the carbon price reaches €50, €60, €70 or €80 per tonne of CO2.