The mining industry continues to be a hotbed of patent innovation. Activity is driven by safety, productivity and cost control. Mine backfilling is widely used to convert resources into reserves, reduce ore dilution, and improve underground working conditions. Backfill mining has several advantages, including the extraction of minerals left in pillars in room and pillar mining, the reduction of the risk of spontaneous rock bursts, the reduction of groundwater contamination when used with binders, and the improvement of mine ventilation. In the last three years alone, there have been over 3,000 patents filed and granted in the mining industry, according to GlobalData’s report on Innovation in mining: mine backfilling. Buy the report here.
However, not all innovations are equal and nor do they follow a constant upward trend. Instead, their evolution takes the form of an S-shaped curve that reflects their typical lifecycle from early emergence to accelerating adoption, before finally stabilizing and reaching maturity.
Identifying where a particular innovation is on this journey, especially those that are in the emerging and accelerating stages, is essential for understanding their current level of adoption and the likely future trajectory and impact they will have.
45+ innovations will shape the mining industry
According to GlobalData’s Technology Foresights, which plots the S-curve for the mining industry using innovation intensity models built on over 81,000 patents, there are 45+ innovation areas that will shape the future of the industry.
Within the emerging innovation stage, tunnel ventilation systems, remote tunnel monitoring, and mine drainage systems are disruptive technologies that are in the early stages of application and should be tracked closely. Lithium recovery, battery metal recycling and tunneling, and anchoring machine are some of the accelerating innovation areas, where adoption has been steadily increasing. Among maturing innovation areas are hydrometallurgical extraction and hybrid industrial vehicles, which are now well established in the industry.
Innovation S-curve for the mining industry
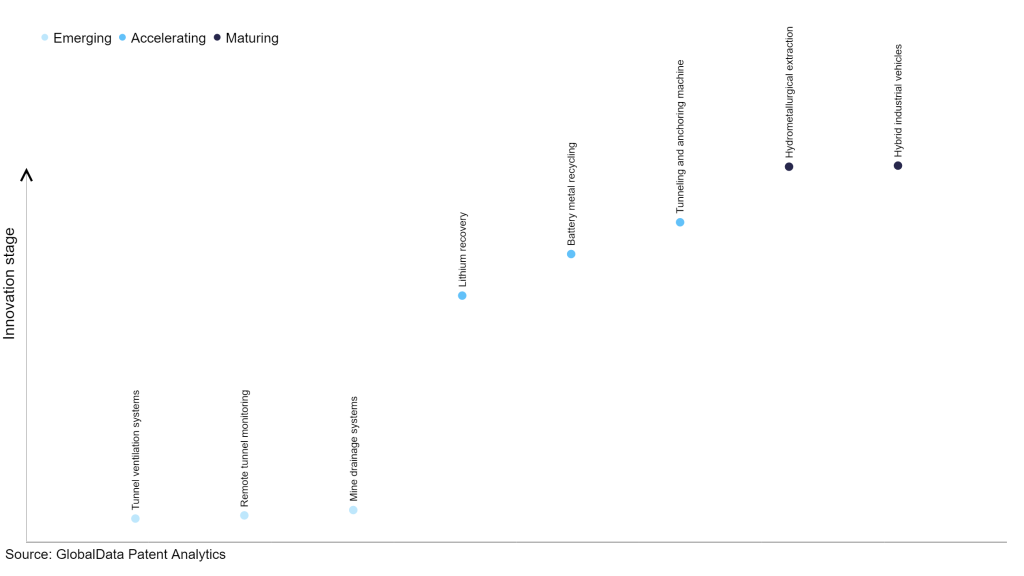
Mine backfilling is a key innovation area in mining
Backfilling is a key operation within underground mining. The backfill material supports the surrounding rock mass, reduces the risk of surface level subsidence, reduces wasteful ore dilution, and creates a safer mining working area. Mining backfill can also be used to dispose of potentially hazardous waste while reducing the environmental impact on the surface by storing backfill waste. The mine backfill process is influenced by the type of mine, tailings, and stope or void location. Heavy equipment is typically used to pump backfill into a stope. Gravity can, however, be used to backfill a shallow mine using dump trucks. The tailings are typically processed at the surface level in large plants before backfilling a mine. A vacuum disc filter is used to extract excess water from tailings, then add a binder to that material using weigh hoppers. High-pressure piston pumps are used to deliver the finished product to the mines, and barricades are placed at the opening of a stope to keep the backfill in place while it cures.
GlobalData’s analysis also uncovers the companies at the forefront of each innovation area and assesses the potential reach and impact of their patenting activity across different applications and geographies. According to GlobalData, there are 140 companies, spanning technology vendors, established mining companies, and up-and-coming start-ups engaged in the development and application of mine backfilling.
Key players in mine backfilling – a disruptive innovation in the mining industry
‘Application diversity’ measures the number of applications identified for each patent. It broadly splits companies into either ‘niche’ or ‘diversified’ innovators.
‘Geographic reach’ refers to the number of countries each patent is registered in. It reflects the breadth of geographic application intended, ranging from ‘global’ to ‘local’.
Patent volumes related to mine backfilling
Company | Total patents (2021 - 2023) | Premium intelligence on the world's largest companies |
State-owned Assets Supervision and Administration Commission of the State Council | 25 | Unlock Company Profile |
Shandong Gold Group | 22 | Unlock Company Profile |
Tian Di Science & Technology | 18 | Unlock Company Profile |
Jinchuan Group | 13 | Unlock Company Profile |
Uni-President Enterprises | 12 | Unlock Company Profile |
Shanxi Tiandi Coal Mining Machinery | 12 | Unlock Company Profile |
Bgrimm Technology Group | 12 | Unlock Company Profile |
Guizhou Kailin Group | 9 | Unlock Company Profile |
China Energy Investment | 9 | Unlock Company Profile |
Tongling Nonferrous Metals Group | 8 | Unlock Company Profile |
Huawei Metal Mineral Resource Efficient Recycling Utilization National Engineering Research Center | 8 | Unlock Company Profile |
Zijin Mining Group | 7 | Unlock Company Profile |
Hebei Iron and Steel Group Mining | 7 | Unlock Company Profile |
Shandong Energy Group | 6 | Unlock Company Profile |
JRI Ingenieria | 6 | Unlock Company Profile |
Daye Nonferrous Metals Group | 5 | Unlock Company Profile |
Yankuang Group | 4 | Unlock Company Profile |
Chongyi Zhangyuan Tungsten | 4 | Unlock Company Profile |
Western Mining | 4 | Unlock Company Profile |
Beijing Energy | 4 | Unlock Company Profile |
Zhongjin Gold | 3 | Unlock Company Profile |
Shandong Hualian Mining | 3 | Unlock Company Profile |
China Minsheng Banking | 3 | Unlock Company Profile |
Wengfu (Group) | 3 | Unlock Company Profile |
Harbin Yonghengxin Technology Development | 3 | Unlock Company Profile |
Guizhou Chenhuida Mining Engineering | 3 | Unlock Company Profile |
AnHui Jinrisheng Mining | 3 | Unlock Company Profile |
Jinneng | 3 | Unlock Company Profile |
Shanxi Coking Coal Group | 3 | Unlock Company Profile |
Jizhong Energy Group | 3 | Unlock Company Profile |
Magang | 3 | Unlock Company Profile |
Shenzhen Zhongjin Lingnan Nonfemet | 3 | Unlock Company Profile |
China General Technology | 3 | Unlock Company Profile |
Guangdong Hongda Blasting | 2 | Unlock Company Profile |
Inner Mongolia Jintao | 2 | Unlock Company Profile |
Shandong Xinjulong Energy | 2 | Unlock Company Profile |
Guizhou Jinfeng Mining | 2 | Unlock Company Profile |
CINF Engineering | 2 | Unlock Company Profile |
Huang Ming | 2 | Unlock Company Profile |
Sinohydro Bureau 9 | 2 | Unlock Company Profile |
China Pingmei Shenma Group | 2 | Unlock Company Profile |
China Gold International Resources | 2 | Unlock Company Profile |
Denison Mines | 2 | Unlock Company Profile |
Zhaojin Mining Industry | 2 | Unlock Company Profile |
Jiuquan Iron and Steel (Group) | 2 | Unlock Company Profile |
Hubei Xingfa Chemicals Group | 2 | Unlock Company Profile |
Jiashi Tonghui Mining | 2 | Unlock Company Profile |
China National Coal Group | 1 | Unlock Company Profile |
China National Chemical | 1 | Unlock Company Profile |
Jin Horoc Nonferrous Metal Group | 1 | Unlock Company Profile |
Source: GlobalData Patent Analytics
China’s State-owned Assets Supervision and Administration Commission of the State Council (SASAC), Tian Di Science & Technology, Shandong Gold Group, and Jinchuan Group are among the leading patent filers in mine backfilling.
Jinchuan Group operates one of China's largest modern mines. The company employs a unique downward hexagonal approach backfill method that includes mechanized mining equipment such as a drill trolley, scarper, and patio drill. The company has constructed independent backfill systems in several mining areas, and approximately 90% of the backfill slurry can be transported by gravity, with only a few areas requiring pressure pumping backfill.
In terms of application diversity, Inner Mongolia Jintao leads the pack, while Tongling Nonferrous Metals Group and Western Mining stood in the second and third positions, respectively. By means of geographic reach, Shandong Energy Group held the top position, followed by Guangdong Hongda Group and Guizhou Kailin Group.
To further understand the key themes and technologies disrupting the mining industry, access GlobalData’s latest thematic research report on Mining.
Data Insights
From
The gold standard of business intelligence.
Blending expert knowledge with cutting-edge technology, GlobalData’s unrivalled proprietary data will enable you to decode what’s happening in your market. You can make better informed decisions and gain a future-proof advantage over your competitors.