In almost every scenario envisaging a world in which governments act to prevent runaway climate change, carbon-free electricity displaces fossil fuels to run our economies. Mobility, heating and even industrial processes all transition to largely run on renewable electricity by mid-century – meaning the future of batteries is inextricably linked to the overall energy transition.
In much the same way the fossil fuel-dominated economy operates via a network of oil and gas pipelines and tanks, conveyance and storage, the electrified world will rely on both transmission lines and batteries to match supply with demand. Variable output from wind and solar power plants will increasingly be stored in batteries.
Lithium-ion batteries similar to those that power mobile phones and laptops will power an ever-growing share of vehicles and provide back up power to homes and offices. Even countries with extensive electricity interconnections with their neighbours, such as the Nordics have with the rest of northern Europe, will find widespread uses for batteries. In countries like the US, which lack an integrated national transmission grid, batteries will be called on to smooth local and regional imbalances between power supply and demand.

The scale of battery deployment required in such a world is staggering. Jut meeting electric vehicle (EV) production targets already announced by carmakers will require 1,000 gigawatt hours (GWh) of global battery manufacturing capacity in 2025, says the International Energy Agency (IEA). Global annual battery production could hit 1,500 GWh by 2030 to meet demand for EVs, based on long-term targets set by governments.
Falling costs
How quickly batteries can displace combustion engines in fossil fuel vehicles, or natural gas peaker plants used to support the power grid, depends on whether economies of scale continue to drive down costs.
The average cost of lithium-ion battery cells has declined by 82% since 2012, according to IHS Markit. The research firm expects the average cost of lithium-ion battery cells to fall below $100 per kilowatt hour (kWh) in 2023 and to $73/kWh by 2030. This figure is the consensus industry benchmark where battery electric vehicles are expected to reach upfront price parity with internal combustion engine cars. Battery costs may fall further still, to $61/kWh by 2030, believe researchers at energy research firm Bloomberg NEF (BNEF).
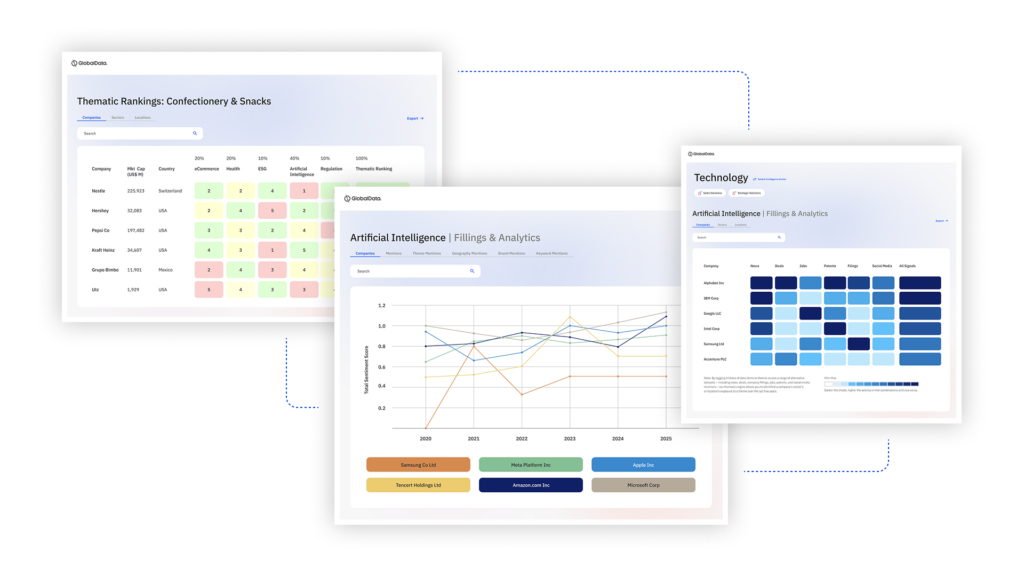
US Tariffs are shifting - will you react or anticipate?
Don’t let policy changes catch you off guard. Stay proactive with real-time data and expert analysis.
By GlobalData“Cost is the name of the game,” says IHS Markit senior analyst Youmin Rong. “Technology advances and competition between different types of lithium-ion batteries is driving prices down. Ultimately, the two major growth markets – transportation and electric grid storage – depend on lower costs to make batteries more competitive with the internal combustion engine and fossil fuel power generation.”
Tesla says it has been so successful in reducing battery costs that it plans to make a $25,000 EV by 2023. A host of improvements to cell design, anode and cathode materials, and cell vehicle integration could reduce the company’s battery manufacturing costs by 56% and boost range by 54% within three years, says CEO Elon Musk.
Lithium-iron-phosphate (LFP) batteries, produced by battery giants BYD and CATL in China, are already under the $100/kWh target, says IHS Markit. The dominant lithium-ion-based battery chemistries used globally – LFP, along with nickel-manganese-cobalt (NMC) and nickel-cobalt-aluminum (NCA) – are all expected to be below $100/kWh by 2024.
Supply of rare minerals
For now, the batteries mostly commonly used in vehicles or in stationary energy storage systems are based on lithium-ion technologies. Chemistries vary but the dominant variations – LFP, NMC, and NCA – use rare, hard-to-source raw materials like lithium, cobalt, nickel and graphite. Industry experts closely monitor the lithium-ion battery supply chain to determine if raw materials will be available in sufficient quantities to meet expected demand for all-electric vehicles and stationary energy storage systems.
In Wood Mackenzie’s ‘base case’ global EV forecast, researchers find the supply of battery raw materials is sufficient over the coming decade, but most markets move into deficit beyond 2030 as EV sales “take off” and comprise 40% of passenger vehicle sales by 2040.
When WoodMac analyses two “accelerated energy transition” scenarios, which assume policymakers take more aggressive action to reduce emissions and hold down rising temperatures globally, researchers find the supply of raw materials is constrained much sooner. Under the “accelerated energy transition” scenario, which would limit global warming to 2.5°C, EVs reach 20% of vehicle sales by 2025 and more than 50% by 2035.
To meet demand in that scenario, the cobalt market would have to double by 2025, and batteries would absorb 30% of global nickel demand by 2030, up from less than 5% today.
“Both scenarios leave us with two simple options: increase supply or decrease demand,” the researchers conclude. “For an accelerated energy transition to succeed in transportation, ‘normal rules’ in areas like capital allocation, governmental support for mining and even globalised supply chains will need a rethink.”
Musk said at Tesla’s September 2020 Battery Day that the company had acquired a lithium deposit near its Nevada gigafactory and would start lithium mining. Tesla claims to have developed a new method to extract lithium from clay deposits. However, details on the process were scarce, and experts are sceptical that Tesla has made a breakthrough discovery. Tesla will also begin recycling batteries in Nevada by the end of 2020.
Fight for global battery dominance
Because the batteries for mobile (vehicles) or stationary (buildings, substations) applications are today based mostly on lithium-centred chemistries, the countries that host lithium deposits, or that have already invested in a lithium-ion battery supply chain, are well positioned to dominate the market – at least over the short term.
BNEF’s inaugural global lithium-ion battery supply chain ranking finds that China has leaped past Japan and Korea to take firm control of the industry until at least 2025. China accounts for 80% of raw material refining, 77% of cell capacity, and 60% of component manufacturing globally, says the report. China is home to 107 of the 142 lithium-ion battery factories already built or under construction worldwide, says a report from Washington, DC-based nonprofit Securing America’s Future Energy (SAFE).
“China’s dominance of the industry is to be expected given its huge investments and the policies the country has implemented over the past decade,” says BNEF head of energy storage James Frith. “Chinese manufacturers, like CATL, have come from nothing to being world-leading in less than ten years.”
Five European countries (Germany, the UK, Finland, France and Sweden) appear in the top ten of BNEF’s 2020 global lithium-ion battery supply chain rankings. The continent has grand battery ambitions. The European Commission, which launched the European Battery Alliance in October 2017, sees the potential for a €250bn annual market by 2025. Just meeting EU demand is estimated to require ten to 20 large-scale gigafactory battery manufacturing facilities.
Swedish battery maker Northvolt has raised €3bn towards the development of two lithium-ion battery cell production gigafactories. Northvolt Ett in Skellefteå, Sweden, which is expected to come online in 2021, will have a production capacity of up to 40GWh. Northvolt Zwei, in Salzgitter, Germany, a joint venture with Volkswagen Group, is scheduled to open in 2024 and to produce more than 20GWh. In September 2020, Oil major Total and carmaker Groupe PSA launched the Automotive Cells Company, a joint venture with financial backing from France and Germany with plans to build a lithium-ion battery manufacturing gigafactory in each country.
For now, the US lags behind in the global lithium-ion battery race – coming in at number six in BNEF’s 2020 global ranking. Just nine of the 142 built or in-the-works lithium-ion battery factories worldwide are planned for the US, says SAFE.
The US lacks a national industrial policy for batteries comparable to those in China or the EU.
“America is 100% dependent on imports for 14 of 35 of the minerals deemed critical by the federal government to the economic and national security of the US,” says SAFE.
In the absence of a national battery push, the private sector is developing battery manufacturing facilities. South Korean conglomerate SK Innovation is building factories in the US state of Georgia that will produce batteries for 300,000 EVs annually at full capacity.
Giga-scale, grid-connected storage
Lithium-ion battery cells aren’t just being used in the growing global fleet of EVs. Project developers and utilities are using batteries to provide flexibility to the grid and to integrate larger shares of renewable energy. On a smaller scale, businesses and homeowners are turning to batteries for back up power peace of mind or to control energy costs. US residential solar leader Sunrun says 20% of the solar power systems it installs nationwide include batteries.
South Australia’s Hornsdale Power Reserve, a lithium-ion battery plant installed by Tesla, is the best known of the first wave of massive mega-battery projects. Recently expanded to 150MW/194MWh, the project earns revenue for its owner, the French energy company Neoen, by providing frequency control and other grid services. Tesla’s ‘big battery’, as the project is colloquially known, is credited with helping prevent outages during grid disruptions and having saved consumers more than €91m in avoided grid operation costs.
The US may be behind in building a domestic lithium-ion battery supply chain, but that hasn’t stopped developers from constructing ever-larger grid-connected battery storage projects. In August 2020, LS Power’s 250MW/250MWh Gateway Energy Storage project in San Diego County, California, dethroned the Hornsdale Power Reserve as the world’s largest battery. In Texas’s deregulated electricity market, nearly 17,500MW of energy storage projects are waiting in the state grid operator’s interconnection queue.
Even larger storage projects are coming. Vistra Energy is replacing a retired natural gas-fired power plant with a 1,500MW/6,000MWh battery project in Moss Landing on California’s Central Coast. Neoen has filed plans to build the Goyder South project, a hybrid wind and solar power plant in South Australia with a 900MW/1,800MWh battery.
Lithium-ion to stay on top – for now
For now, most of the batteries installed in vehicles, and deployed to support grids, around the globe will be lithium-ion.
“For the foreseeable future, in terms of EVs, iti s all lithium-ion,” says Gavin Montgomery, research director, battery raw materials at Wood Mackenzie. “Nearly every battery factory or cell factory being built anywhere in the world at the minute is a lithium-ion battery factory. That family of batteries will be around for quite a long time.”
There will be advances made, he adds, with different generations of lithium-ion batteries coming online and the eventual emergence of so-called ‘solid-state’ batteries. Energy storage systems could see more diversity in the types of batteries used as space and weight are not as much of a factor for stationary battery applications as they are for EVs and personal electronics. Technologies like vanadium flow batteries, which use tanks of electrolytes to store and release energy, could take hold in the market in the future.
“I don’t think wea re moving away from lithium-ion,” says Montgomery. “Lithium-ion is dominating because all the R&D is in lithium-ion these days and the costs are coming down.”
Part two of this series will examine the environmental, social and health impacts of lithium-ion batteries.