The mining industry continues to be a hotbed of patent innovation. Activity is driven by the need for improved productivity, safety, cost control and sustainability, with the growing importance of recycling in order for sufficient metals and materials to be available to support the global energy transition. In the last three years alone, there have been over 3,000 patents filed and granted in the mining industry, according to GlobalData’s report on Innovation in mining: battery metal recycling. Buy the report here.
However, not all innovations are equal and nor do they follow a constant upward trend. Instead, their evolution takes the form of an S-shaped curve that reflects their typical lifecycle from early emergence to accelerating adoption, before finally stabilizing and reaching maturity.
Identifying where a particular innovation is on this journey, especially those that are in the emerging and accelerating stages, is essential for understanding their current level of adoption and the likely future trajectory and impact they will have.
45+ innovations will shape the mining industry
According to GlobalData’s Technology Foresights, which plots the S-curve for the mining industry using innovation intensity models built on over 81,000 patents, there are 45+ innovation areas that will shape the future of the industry.
Within the emerging innovation stage, tunnel ventilation systems, remote tunnel monitoring, and mine drainage systems are disruptive technologies that are in the early stages of application and should be tracked closely. Lithium recovery, battery metal recycling and tunneling, and anchoring machine are some of the accelerating innovation areas, where adoption has been steadily increasing. Among maturing innovation areas are hydrometallurgical extraction and hybrid industrial vehicles, which are now well established in the industry.
Innovation S-curve for the mining industry
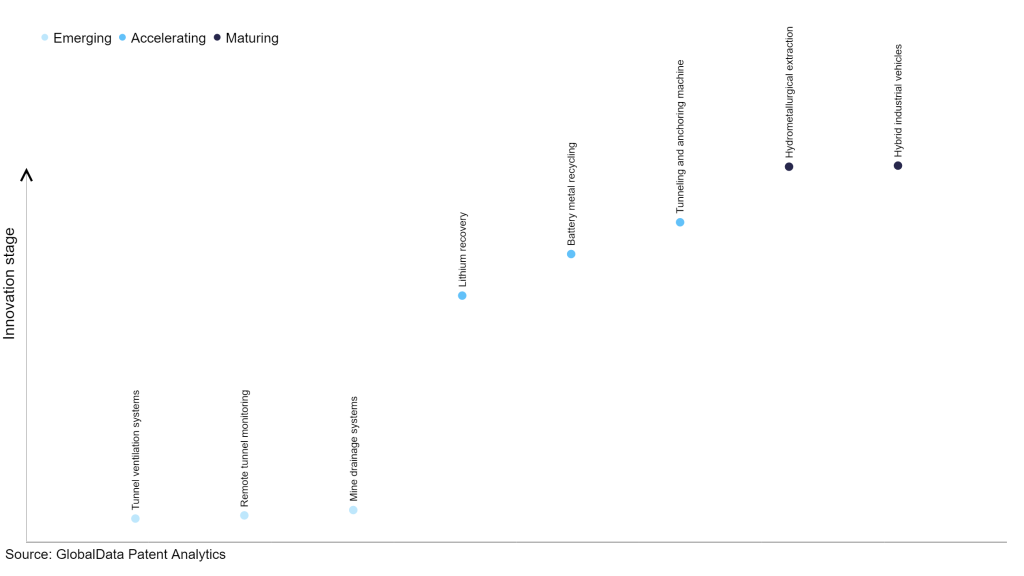
Battery metal recycling is a key innovation area in mining
Batteries contain a number of heavy metals including some precious metals. Recycling of batteries to extract these metals is a fast-growing industry in itself, especially in growing economies. For example, the nickel in nickel-metal hydride batteries is recovered to make steel. Cobalt, nickel and copper can be recovered from lithium batteries. Mercury is recovered from mercury cell batteries and the decontaminated steel fraction is used to make steel. Battery recycling industry leaders are offering low-carbon mechanical and hydrometallurgical technologies to recycle battery materials in order to recover lithium, cobalt, manganese, and nickel for reuse in the production of new batteries.
GlobalData’s analysis also uncovers the companies at the forefront of each innovation area and assesses the potential reach and impact of their patenting activity across different applications and geographies. According to GlobalData, there are 30+ companies, spanning technology vendors, established mining companies, and up-and-coming start-ups engaged in the development and application of battery metal recycling.
Key players in battery metal recycling – a disruptive innovation in the mining industry
‘Application diversity’ measures the number of applications identified for each patent. It broadly splits companies into either ‘niche’ or ‘diversified’ innovators.
‘Geographic reach’ refers to the number of countries each patent is registered in. It reflects the breadth of geographic application intended, ranging from ‘global’ to ‘local’.
Patent volumes related to battery metal recycling
Source: GlobalData Patent Analytics
Leaders in battery metal recycling include ENEOS, JFE, and Bain Capital. ENEOS has pioneered the recovery of high-purity metal salts from automotive lithium-ion batteries. In 2020, the company began operating bench-scale equipment installed in its Hitachi Works Technology Development Center for technological and system development for closed-loop recycling, in which resources are recovered from used automotive lithium-ion batteries and reused as raw materials for new automotive lithium-ion batteries. Furthermore, in 2021, the company started trials for nickel sulphate recovery and introduced a new process at its Tsuruga Plant based on this bench-scale equipment.
ENEOS collaborated with Redivivus, a lithium-ion battery recycling startup, in January 2023 to accelerate the development of Redi-Shred®, a passivation technology to safely process end-of-life batteries at any state of charge or health.
JFE recycles used batteries, which are collected as general waste through public waste collection and are melted in high-temperature electric furnaces, allowing for the extraction of iron, manganese, and zinc, which can then be reused for other purposes.
In terms of application diversity, Hyundai Motor leads the pack, while Corporacion Nacional del Cobre de Chile and Heraeus stood in the second and third positions, respectively. By means of geographic reach, Rio Tinto held the top position, followed by Jeffery Steel and Hyundai Motor.
To further understand the key themes and technologies disrupting the mining industry, access GlobalData’s latest thematic research report on Mining.
Data Insights
From
The gold standard of business intelligence.
Blending expert knowledge with cutting-edge technology, GlobalData’s unrivalled proprietary data will enable you to decode what’s happening in your market. You can make better informed decisions and gain a future-proof advantage over your competitors.